
WEST SIDE SHADY GROVE
ROCKVILLE, MD
BEN CARRUTH
CONSTRUCTION MANAGEMENT
BUILDING STATISTICS
General Building Data:
-
8010 Gramercy Road
-
Rockville, MD 20850
-
Mixed Use - Multifamily Residential Building
-
510,957 GSF
-
6 Stories
Primary Project Team:
Owner: EYA and Bozzuto Development Company
General Contractor: Bozzuto Construction Company
Architect: KTGY Group, Inc.
Structural Engineer: Tadjer-Cohen-Edelson
MEP Engineer: SSA Engineering, LLC
Civil Engineer: VIKA Maryland, LLC
Landscape Architect: Studio39
Interior Design: Forrest Perkins
Construction Dates:
November 2015 – September 2016
Cost Information:
Building Original Contract: $51,002,275.00
Project Delivery Method:
Design-Bid-Build
Architecture:
West Side Shady Grove was designed as a multi-family housing apartment complex with two story commercial space on the frontage of the building on Gramercy Boulevard. The building also includes a four story open parking garage. The residential portions of the building range from four to six floors; six floors where the building includes commercial space, as four floors of dwelling units rest on a two story concrete podium. The building includes two interior courtyards, one of which contains a swimming pool.
The site is located in Rockville zoning area A-2 under Planned Development.
The major applicable codes are as follows:
-
2012 International Building Code
-
2012 International Mechanical Code
-
2012 International Plumbing Code
-
2008 NFPA National Electric Code
-
2010 International Fire Code
-
2012 International Energy Conservation Code
-
2012 International Fuel Gas Code
-
2010 Americans With Disabilities Act
-
COMAR 05.02.02, ADAAG & FFHAG (State Adoption)
-
LEED For Home Mid-Rise Silver Level
Building Enclosure:
There are multiple types of facades on this building, which means there are multiple building enclosures. The roofing is Thermoplastic Olefin (TPO) layered on ¼” dens-deck as seen in Figure 1.
The two main types of facade are fiber cement panels and colored brick veneer. The fiber cement panels (Hardi Panels) are connected to the exterior sheathing by ⅜” x 1 ½” furring as seen in Figure 2.
The brick facade is mostly
found on the commercial spaces under the concrete podium and is attached with adjustable anchor ties as seen in Figure 3. Both facades can be seen in the west elevation in Figure 4.
Sustainability Features:
West Side Shady Grove, while under construction, is targeting LEED Silver as it’s final sustainability goal. The building incorporates a few sustainable features including LED lighting and Biofilters. The Biofilter retention systems are a major stormwater management system found all around the building and in the courtyards. The biofilters collect rain and storm water from the building and stores it in concrete retention planters that are layered soil and other sediment to filter the stormwater before it is returned to the sewer main. A section of a typical Biofilter can be seen in Figure 5.
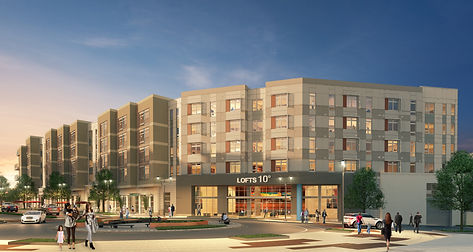

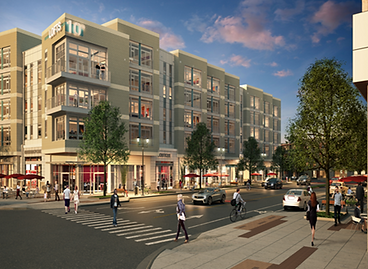

Figure 1

Figure 2

Figure 3

Figure 4
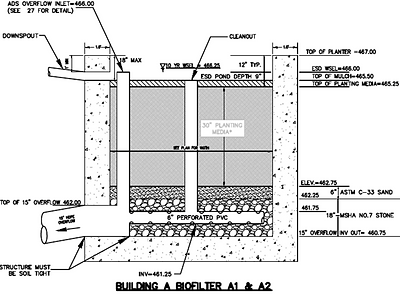
Figure 5
Building Statistics 2
Construction:
The construction of West Side Shady Grove Project broke ground in November of 2015. With Bozzuto Construction Company as the chosen General Contractor to oversee construction, an aggressive 23 month schedule was developed to have the 511,000 square foot mixed-use multi family finished by September of 2017. However, with Bozzuto Management leasing in mind, the first phase of the building will be turned over earlier in 2017 around April in order to start leasing the building out to residents. The budget developed was $51M and a major goal of the owners and GC was LEED Silver certification.
The delivery system chosen was design-build, allowing the owners, architect, and engineers to finish details of design well past the beginning of construction. The GC, Bozzuto Construction, holds lump sum contracts with all subcontractors which are typically long form contracts for any subcontract over $250,000 and short form for any under $250,000. All subcontractors are also required to have a certification of insurance in order to perform work on site.
A notable aspect of the construction sequence on this project that stands out is the “tunnels” that have been left out of three sections of the building to allow vehicle and equipment access to both courtyards and the East side exterior of the building. Two floors in building sections B, E and D were left unconstructed and the concrete slab on grade was reinforced in these areas to support construction loads. This was done because the owners wanted to be able turnover the “front” section of the building (Phase 1) which includes the leasing office and roughly half of the dwelling units. Normally the building would be constructed from the “back” out which would not require any special access. The tunnels will be filled in once all heavy equipment work is finished in the courtyards. See Figure 1 for a photograph of the front two tunnels in section E and then section D through the first tunnel.
Electrical:
Located in the Southeast corner of the building, under building section A, a utility transformer connects to the buildings main switchboard providing 3500 A. This is distributed to the secondary electrical rooms, two located on each floor, with 100kVA transformers that distribute to the corridors and dwelling units.
Structural:
The structural system for West Side Shady Grove begins with a 6” to 9” slab on grade, 9” where the construction tunnels were left open for construction traffic. The two story concrete podium that can also be seen in Figure 1 is 12” thick and is supported by 22” by 22” reinforced concrete columns. The remainder of the building either sits on the elevated podium or on the slab on grade and is entirely wood framed. The typical span trusses are 18” open web-wood floor trusses at 12” to 24” on center.
Mechanical:
The primary mechanical system that services the dwelling units consist of a range of rooftop condensers, one for each dwelling unit. They range from 17,800 to 34,200 MBH depending on the size of the dwelling unit. They are distributed into the building through duct shafts and then spread to the units in ducts contained in the ceiling. Since each unit is assigned its own condenser, variable temperature control is available through one thermostat per unit.
Fire Protection:
The fire protection system in this building is a dry sprinkler system with all of the building in sprinkler coverage. The sprinklers are fed by a 6” standpipe from each stair tower or in some locations duct shafts and these mains feed into typically 2 ½” plastic corridor pipes and finally to typically 1 ¼” feeder to each room. Each sprinkler is specified to have a maximum flow of 500 gpm and every room in the building contains pendant type sprinkler heads.
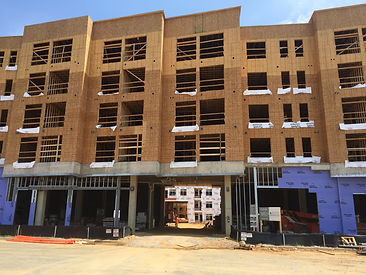
Figure 1